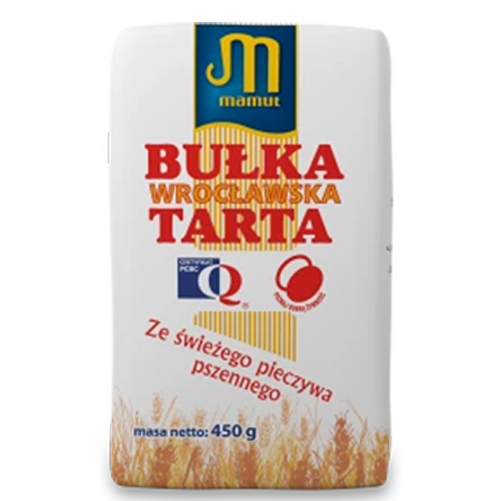
Packaging process significantly improved
MAMUT POLSKA S.A. has been in existence for over 150 years. Today it is one of the largest Polish bakeries and specializes in the production of long-life bakery and confectionery products. MAMUT POLSKA S.A. is the market leader in breadcrumbs, rusks and croutons and sells through three strategic channels: retail, B2B and HoReCa (hotel, restaurant and catering).
The wide range and excellent taste of the products have won the recognition and sympathy of consumers at home and abroad. The company‘s priority has always been constant development based on global food trends and the implementation of the idea that high-quality products are not a luxury, but a standard. Over the years, this approach has led to numerous awards and successes, including the Q quality mark for Wrocławska bread crumbs and the Meet Good Food awards for Wrocławskie sponge cookies and rusks.
Innovative packaging technology for highest quality
The market glamour and wide recognition of MAMUT brand would not be possible without full transparency and safety of production processes, confirmed by ISO:9001 and FSSC 22000 certificates, and supported by wise choices of processing and packaging equipment.
The machinery at the bakery in Wrocław was recently expanded to include a new, modern ROVEMA SBS 250 packaging machine, which is designed for forming and filling high-quality block bottom bags and is equipped with a high-precision auger dosing system. The packs are made from heat-sealable, compostable FSC paper from the flat film web and convince with their excellent sealed seam quality.
The packaging project carried out by ROVEMA and MAMUT was a major challenge for both parties. The general aim was to improve logistics and ensure the full safety of one of the leading products – breadcrumbs. Before the cooperation, the product was packed in traditional prefabricated paper bags, which were sealed with adhesive after filling. Such pre-made bags are very popular with bakeries and flour manufacturers all over the world. They are proven and safe, but the introduction of the new ROVEMA technology has significantly improved the packaging process for breadcrumbs.
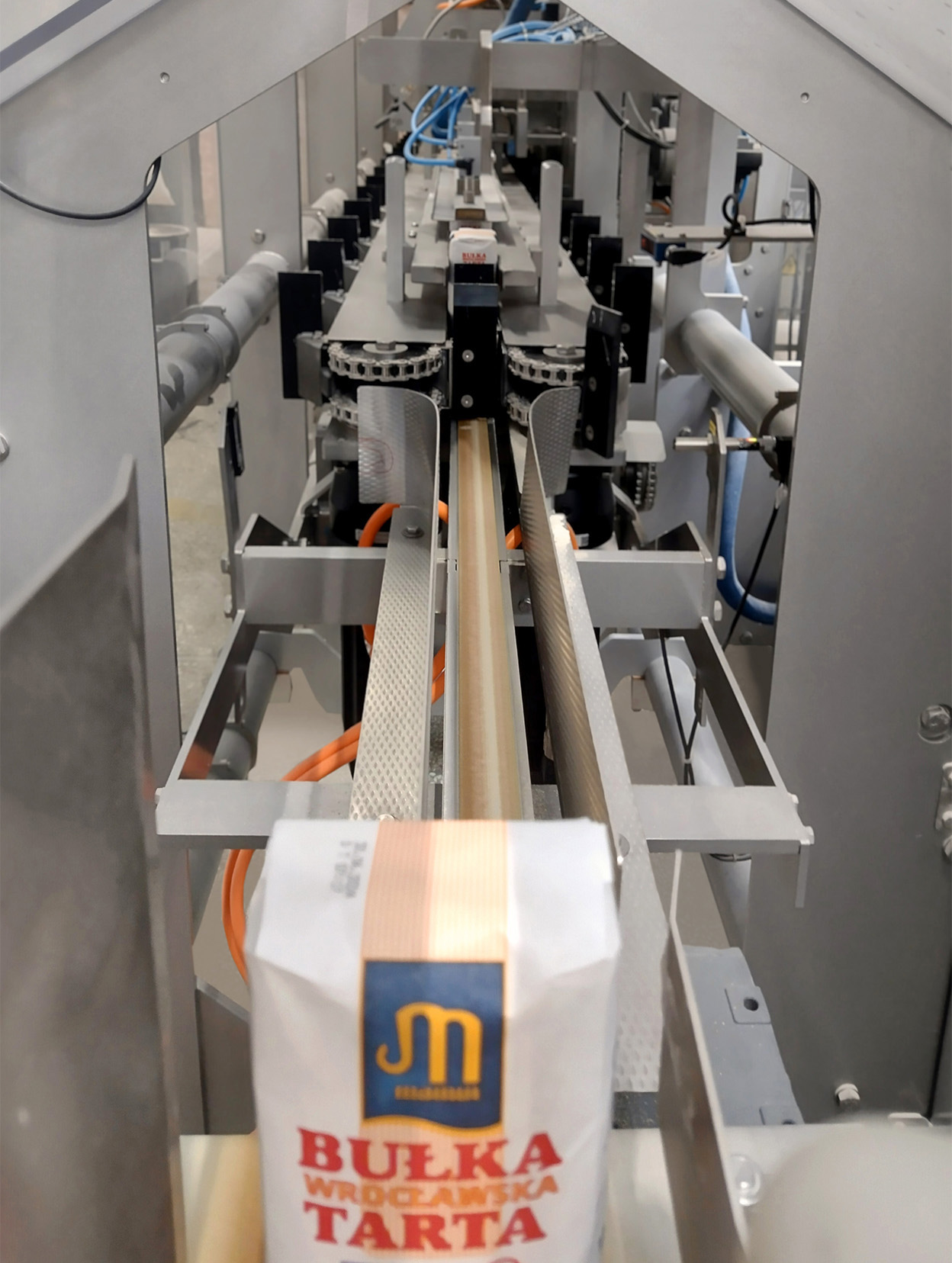
7 convincing reasons
to switch from pre-made bags to bags from the flat film web
Improved machine availability due to reduced susceptibility to process faults (more uptime)
More compact machine with smaller footprint compared to machines for pre-made bags
Low-dust packaging process with less product loss
Possibility to use thinner packaging materials
Lower packaging material costs
Easy storage and handling of packaging materials
Clean printing of the pouches, e.g. with best-before date, is easily possible
Want to optimise your packaging process?
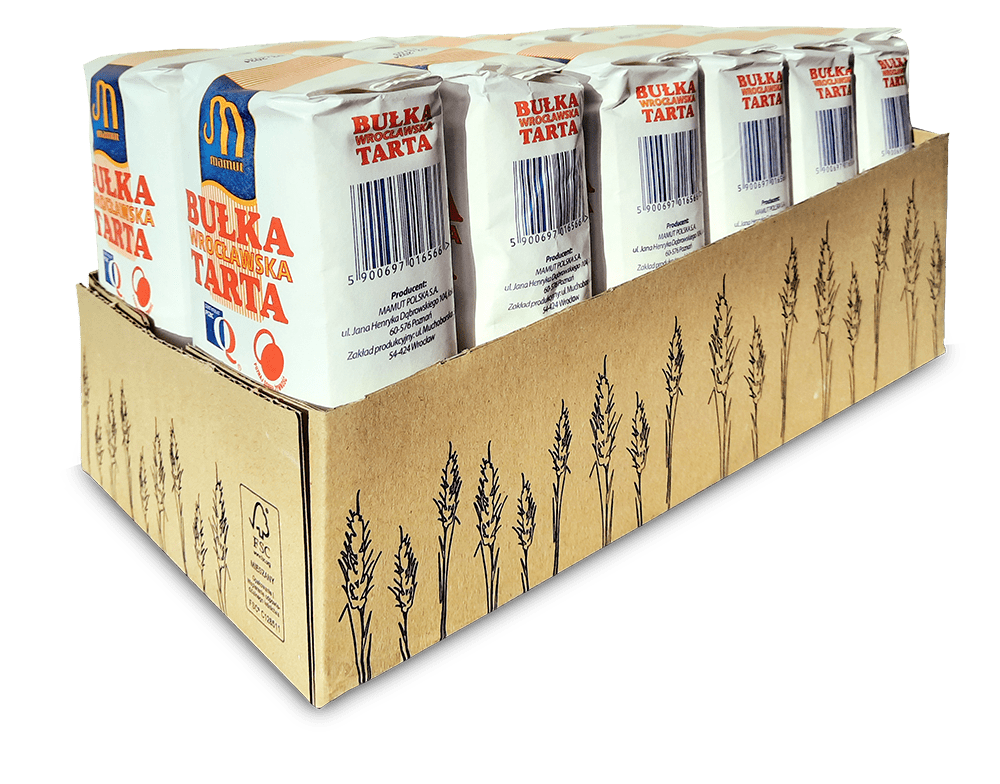
Shelf presentation and transport packaging
Like flours, breadcrumbs are staple foods. They are usually presented at the POS in common and proven packaging forms such as block bottom bags. For transportation, the bags are often placed on simple cardboard trays, wrapped in shrink film and stacked on pallets. It is important that all packaging has the same height and can be stacked stably. An important success factor of the packaging project was to achieve a uniform filling level of the bags and a maximum reduction of air inside the block bottom bags.
With over 65 years of experience in the packaging industry and a strong team of packaging experts, ROVEMA knows how to deal with such requirements and lead projects to success. Good teamwork, high-performance and reliable packaging machines and services and a safe, modern working environment form the basis for the company's success. Added to this is the clear focus on strong, long-term partnerships with customers and suppliers such as packaging manufacturers.
Five steps to perfect packaging
The MAMUT breadcrumbs project began with an in-depth analysis of the packaging task between the manufacturer and ROVEMA. MAMUT supplied the original breadcrumbs in order to assess all the important project parameters such as dosing accuracy, the shape and size of the bags, their air content and, above all, the tightness of the sealing seams. Once all the specifications and objectives had been defined, the next step in the project planning was taken.
After analyzing and defining the requirements, it was checked which reliable partner could supply suitable packaging material. The material was to be a recyclable, compostable and heat sealable FSC paper, supplied in the form of a film roll for vertical processing on the VFFS machine. Three suppliers were able to meet the requirements, and the next step was to test the material.
In total, paper packaging materials from three suppliers were sent to the company headquarters in Fernwald, Germany, for comprehensive testing in the application test. All important project parameters were taken into account in the application tests:
- dosing accuracy
- the uniformity of the bags (shape and size)
- the air content in the pouches
- the quality and tightness of the sealing seams, particularly in the top area of the bag
This first test phase was absolutely crucial for choosing the right paper supplier and for selecting the optimum packaging material. This is because heat-sealable papers – despite having similar specifications – can have very different properties and behave differently on the filling tube and between the sealing jaws of the packaging machine. Some papers ran easily over the forming shoulder, others generated too much friction and tore. The tightness and strength of the sealing seams was also not the same everywhere. Another surprise was a waterbased print, which sometimes caused tears on the packaging material during heat sealing. Fortunately, the paper supplier was able to solve this problem within a few days so that the project schedule could be met without any major delays.
After this in-depth review of paper packaging materials and their manufacturers, it was clear that the final partners for the project would be the two companies MONDI and SILBO, whose proactive approach throughout the process contributed significantly to the project’s success. The global paper and packaging manufacturer MONDI supplied the paper, while Polish partner SILBO used advanced printing and coating technology to transform the MONDI base paper into the final packaging material, which is vertically converted on the ROVEMA machine and looks great on the shelf.

ROVEMA experience center
Every year, more than 100 packaging material, performance and application tests are carried out in the company's own technical center. Over the past decades, an immense knowledge of packaging materials, pouch shapes and packaged goods has been built up, from which ROVEMA customers benefit in the long term.
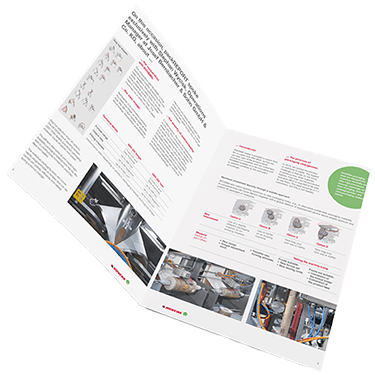
Short profile of the case study
Co-operation partner: MAMUT POLSKA S.A.
Packaging material partners: SILBO Sp. z o.o. Opakowania, Mondi plc
Machines used: Brick Pack Machine SBS, Auger Doser SDH